In this age of visual orientation, the fashionable window design of brands is especially important. A well-designed window not only shows the brand’s design concept and product features, but also gives potential customers a strong visual impact and aesthetic experience. Among the various decorative elements, electroplated window props have become a favorite tool for many brand visual merchandisers because of their unique metallic texture and luster effect, reflecting the simplicity and modernity of contemporary design.
Here sharing some typical brands window designs with electroplated window props.
Gucci Visual Window Display / Store Interior Design / Store Front and Entrance Visual Merchandising Display with Electroplated and LED Lighting Luggage Stacked
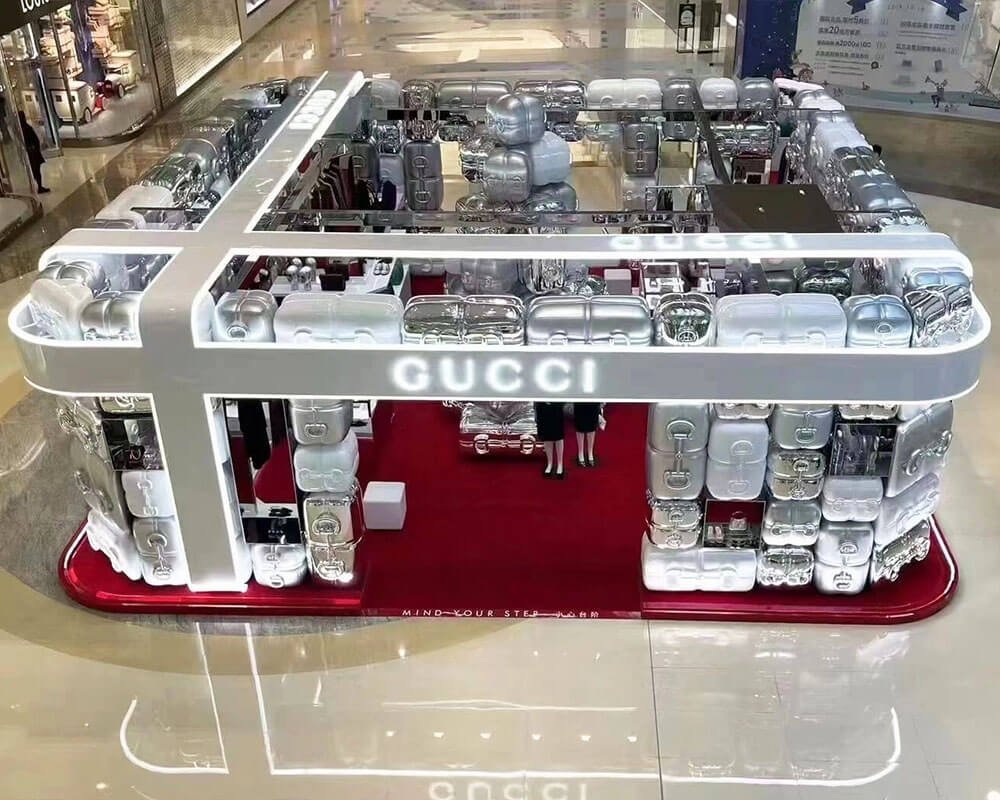


Michael Kors Store Window Design with Electroplated gold chain props, which not only reflect the brand positioning, but also the perfect realization of the visual marketing effect.




The unique plating mirror red is one of popular colors for choosing in fashion retail display.


It is not difficult to realize that mirrored window props never go out of fashion and it is also the one of the representatives of fashion that cannot be absent.Today we would like to introduce a best material for plating in different colors. Here mainly focus on the advantages and disadvantages of Electroplating fiberglass props, as well as plating process, so that your visual merchandisers can understand more about the effect of the presentation,and VM solution ideas for the whole shop window design!
Now, Let’s start with the advantages and disadvantages of Electroplated FRP props:
1. Eye-Catching Attractive Appearance
After Plating, it can show a metal-like mirror effect,which has a very high gloss and decorative finish.-We will mention the detailed process later.
2. Lightweight and high strength
FRP itself has the characteristics of lightweight and high strength, compared with metal with the strength can be comparable to steel. This makes the FRP plating supports even if the shape is complex, not too bulky, transportation and display are more convenient.
3. Good processing performance
FRP can be made into a variety of shapes through molding and other processes, whether it is a simple sphere or complex geometric modeling, which can show the elegant and stylish texture, to meet the demand for customization.
4. Strong adhesion of Chrome Plating Layer
After plating, the surface of FRP forms a dense metallic chrome coating, which is well sealed and can effectively prevent corrosion, and can be maintained in good condition for a long time even in humid environments. (VmDisplay’s electroplated coating can be maintained for 2 years outdoors and 10 years indoors).
5. The color of plating coating is unlimited
You can choose any plating color according to the theme tone of VM projects, which is wider than the choice of metal PVD. If you want red, green, black mirror finish and so on – just provide Pantone number
Of course, there are two sides to everything, here are the disadvantages of fiberglass plating:
1. Higher processing cost than spray painting
Although the cost of FRP molded product itself is not high, but the subsequent vacuum plating process is relatively complex, requiring high equipment and technology investment, resulting in high overall processing cost. However, the total cost is still lower than that of plating metal products.-PVD
2. Product dimension limitation
Which is the size of vacuum plating equipment limitation. VmDisplay Ltd.could offers the largest vacuum plating equipment in China for plating fiberglass and plastic products, that highest up to 210cm and widest 160cm. (Note: I know you will say Nano Spray Plating, but they are really different. Later we will post another article to explain the differences)
After understanding the advantages and disadvantages, I am very happy to share the whole process of vacuum plating of FRP products, which specifically shows our high-end quality and excellent craftsmanship!
Step 1: Surface Preparation
The success of any coating process depends firstly on the surface treatment of the substrate. Good pre-treatment can effectively remove surface oils, oxides, etc., and lay a solid foundation for the subsequent coating process.
For FRP substrate, the commonly used surface treatment includes:
Acid washing: dissolve the impurities and oxides on the surface of the substrate by soaking in acid to ensure that the plating can be firmly adhered to.
Spray primer coating: It must confirm smooth touching finish without any Pinholes and lumps.This process needs to go through 2-3 times of repairing, grinding and polishing to ensure completed smooth.
Step 2: Pre-Treatment of Vacuum Coating
It still needs to do Pre-Treatments to prepare for Vacuum Coating,
It will be arranged to spray with UV primer coating and High temperature baking with UV light to increase the adhesion of the Vacuum plated coating (this step is very important and critical to ensure that the plating finish is high quality and free of impurities afterwards. This is also a process that is missing in other factories).
Here is the pictures for UV lighting with high temperature baking process:

Step 3: Go into Vacuum Machine for Plating
Once the preliminary preparations have been made, the actual palting process can begin. Vacuum chromium plating on FRP is mainly done by DC magnetron sputtering.
Without going into the details of how the chrome is chemically adsorbed on the surface of the product, the most important thing is the vacuum plating equipment, VmDisplay Ltd. can provide two plating furnaces up to 210cm in height and 160cm in width, which allows simultaneous plating of large-sized products and ensures high quality of the chrome layer and also ensures the delivery time of the project.
We are the only factory in China that can provide Vacuum plating for large size FRP products in different colors and ensure mirror-like plating.


Step 4: After-treatment
After the chrome plating is completed, a series of post-treatments are required to refine and adjust the quality of the chrome layer.
After the chrome plating is completed, a series of post-treatments are required to refine and adjust the quality of the chrome layer.
1. If you want any other color plating surface, we are able to spray a color coating after the high quality chrome layer.
2. After drying, it must add a layer of clear UV protective paint to ensure that the color will not fade for about 10 years indoors and 2 years outdoors.



Through the above processes, from surface pre-treatment to vacuum plating coating to post-treatment and inspection, each process is delicate and strict, and each is indispensable. Only through strict control of the entire process can the FRP material obtain an elegant and durable chrome plating with a desirable metallic luster. This is the craftsmanship behind the vacuum chrome plating of FRP, which creates a high level of quality for the product that will never fade with a meticulous attitude. The quality of the coating and the richness of the colors are used in a variety of high-end props.
Here you may mention the Nano Spray Plating, but i would like to say the whole process of vacuum plating is really not the same as nano spray plating. Although it has not the dimension limitations for Nano spray plating, the quality of the plated layer is much lower than vacuum plating, and will be easy to peel off because there is no adhesion on finish.
For the differences between Vacuum plating and Nano Spray plating, we will offer another detail blog for showing. Of course, if you have some props or any projects need the mirror plating finish, just contact us here for more VM solutions and quote.